3D printing powders and polymer resins market by type
Market Overview of 3D Printing Powders and Polymer Resins
The global market for 3D printing powders and polymer resins is expected to grow from USD 7.91 billion in 2023 to USD 18.60 billion by 2030, at a CAGR of 13% during the forecast period.
The use of powdered material as the base material for an object is called powdered. 3D printing. To create the desired object, the powder is usually selectively melted or bonded layer by layer. Powders can be made from a wide variety of materials, including ceramics, metals (such as titanium, aluminum, or stainless steel), and even some types of plastic. The purpose and characteristics of the finished product determine which powder material is better. Electron beam melting (EBM) and selective laser sintering (SLS) are two powder-based 3D printing methods. While the electron beam is used in EBM to melt the powder, the SLS uses a laser to selectively sinter or fuse the powder particles together.
Liquid photopolymer resin is the main material used in polymer resin 3D printing. Resin printing is often done by photopolymerization, a procedure in which the material hardens when exposed to light. Different resin formulations are available, each with unique qualities such as strength, flexibility, or clarity. Standard resins, flexible resins, durable resins, and high-temperature resins are examples of common varieties. Stereolithography (SLA) and Digital Light Processing (DLP). While a digital light projector is used in DLP to project the entire layer at once, SLA uses a laser to selectively cure the resin layer by layer. Prototyping, dentistry, and the jewelry industry are among the fields where polymer resin 3D printing is widely used.
The manufacturing sector has undergone a change thanks to 3D printing technology, which has brought new and efficient methods for creating complex and personalized items. Printing powder and polymer resin are two of the most important ingredients in 3D printing.
The main component of some 3D printing methods, such as selective laser sintering (SLS), is the printing powder. This method creates a three-dimensional object by selectively joining layers of powdery material using a laser. Usually, materials such as nylon, polyamide, or metal alloys are used to make printing powder. The value of powder for printing lies in its ability to offer a flexible and affordable means of creating durable, detailed components. Conversely, polymer resin plays a crucial role in 3D printing, digital light processing (DLP), and stereolithography (SLA) processes. These treatments use a liquid resin that hardens layer by layer when exposed to light.
Different polymer resin formulations are available, each with specific qualities such as strength, flexibility, or clarity. Resin's ability to create complex objects with smooth surfaces and high resolution clearly shows how important it is for 3D printing. Because polymer resins can be used with such precision and accuracy, SLA and DLP technologies are widely used in dentistry, jewelry manufacturing, and prototyping. The combination of printing powder with polymer resin demonstrates how versatile 3D printing is and how it can be used in a variety of industries and applications. The strength and adaptability of printing powders in SLS and the ability to create complex and detailed designs using polymer resins in SLA and DLP are just two examples of how these materials greatly increase the flexibility and ingenuity that 3D printing technologies provide. The possibilities and potential uses of 3D printing in various industries are likely to continue to expand as technology advances through the creation of new and improved printing powders and polymer resins.
ATTRIBUTE | LEARN MORE |
Period of study | 2020-2030 |
Base year | 2022 |
Estimated Year | 2023 |
Projected Year | 2023-2030 |
Historical period | 2019-2021 |
Units. ism | Cost (billions of US dollars) Volume (kilotons) |
Segmentation | By Type, Application and Region |
By Type |
|
By Application |
|
By Region |
|
Market Segmentation Analysis of 3D Printing Powders and Polymer Resins
The global market for powders and polymer resins for 3D printing is divided into two segments based on types and applications. According to the type, they are divided into powders and polymer resins, in which the powders segment has the largest market share.
Metals, ceramics, and polymers are just a few of the materials that are included in the category of 3D printing powders. Metals such as titanium, aluminum, and stainless steel are commonly used in a variety of industries that require components of exceptional strength and durability. Powder 3D printing is very versatile and can be used in a variety of industries, including healthcare, automotive, and aerospace, especially when combined with techniques such as selective laser sintering (SLS). The growing demand for metal powders can be attributed to their ability to create functional prototypes and complex shapes. Polymer resins are an integral part of liquid-based 3D printing technologies such as digital light processing (DLP) and stereolithography (SLA). There are various materials available in the polymer resin market, such as photopolymer resins that harden when exposed to light. These resins are ideal for the production of consumer goods, jewelry, and dental products because they have a high degree of detail and surface finish. Continuous innovation in the polymer resin industry is evident in the creation of customized formulations to meet specific needs, such as biocompatibility, flexibility and transparency.
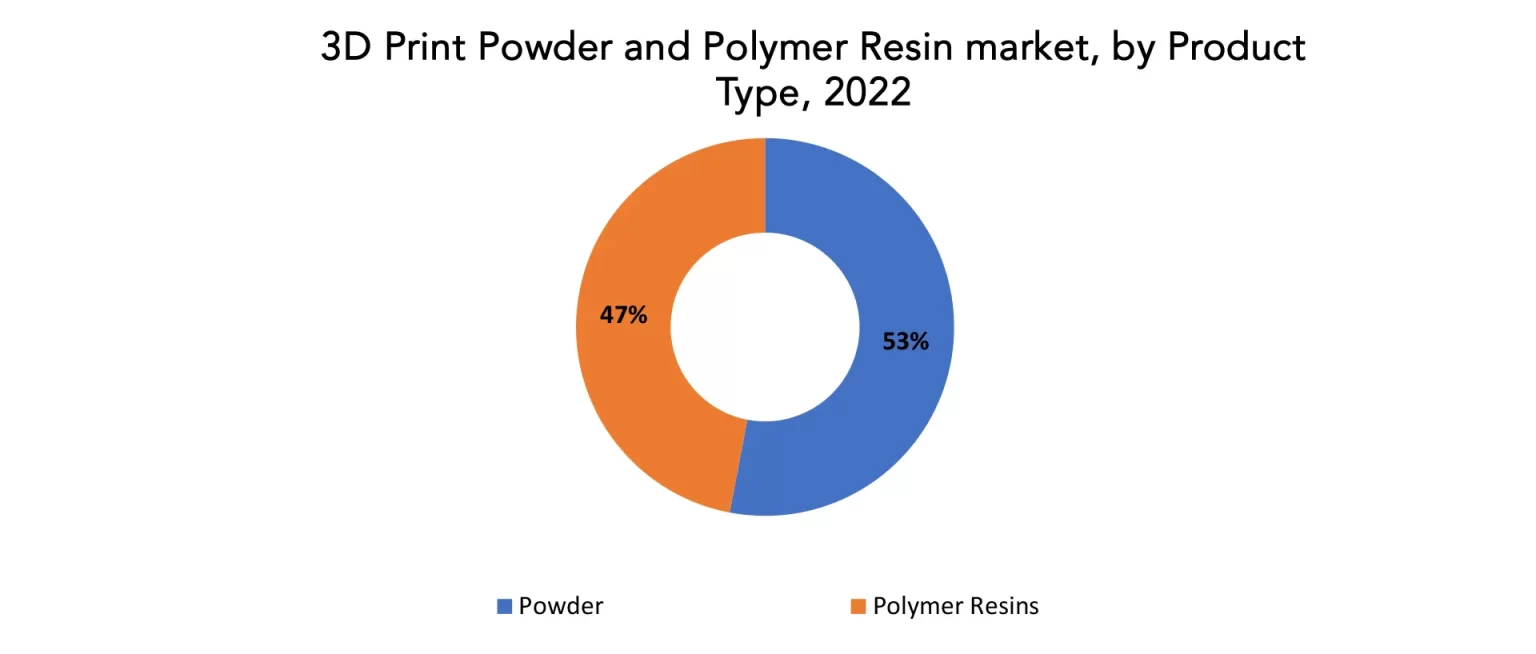
In terms of application, it is divided into healthcare, aerospace, and defense, in which the aerospace and defense industry has the largest market share.
The market for 3D printing powders and polymer resins is expected to increase significantly due to the influence of the aerospace, defense, and medical sectors. R&D efforts focus on solving specific industry challenges, including creating materials that meet stringent performance requirements in the aircraft industry or have the necessary approvals for medical use. These industries are expected to use 3D printing more frequently as technology advances, leading to an increase in demand for specialty powder and resin ingredients. In addition, the customization capabilities of 3D printing are perfectly suited to the special and complex needs of the aerospace and defense industries, as well as healthcare.
Both powder and polymer materials are widely used in the aerospace and defense industry for 3D printing to create strong and lightweight components. Due to their strength-to-weight ratio, metal powders such as titanium and aluminum alloys are preferred for use in the aerospace industry. SLS, or Selective Laser Sintering, is a type of powder-based 3D printing that helps reduce weight and improve fuel efficiency in airplanes and spacecraft by producing detailed and complex parts. Prototypes, tools, and parts for aerospace and defense systems are made from polymer resins, especially those that are resistant to high temperatures and durable. One of the main advantages of 3D printing in this industry is its ability to quickly prototype and repeat designs, which helps create creative and efficient structures. The use of polymer resins for 3D printing has become quite popular in the healthcare industry for applications such as dental products, prosthetics, medical device manufacturing, and anatomical models. Due to their superior resolution and biocompatibility, photopolymer resins are widely used in the production of patient-specific precision medical implants. For example, surgical planning and training are facilitated by 3D printed models of organs or tissues based on patient images. In addition, the dental sector benefits from the ability to customize 3D printing, which allows crowns and dentures to be produced that fit together perfectly. Materials with improved biocompatibility and sterilizing capabilities are in high demand in the healthcare sector, in the production of 3D printing powders and polymer resins.
3D Printing Powders & Polymer Resins Market Trends
- Creating customized materials to meet the specific needs of the industry is becoming increasingly popular. This includes materials with special qualities, including conductivity for electronics, high temperature resistance for the aerospace industry, and biocompatibility for healthcare.
- The use of complex metal powders in metal 3D printing is becoming more and more common. The aerospace and automotive industries, where there is a growing need for lightweight and highly durable components, are the main drivers of this trend.
- The industry is seeing a shift in focus on eco-friendly materials and sustainable practices. This includes researching materials with less environmental impact, recycled powders, and bio-based polymers.
- Nowadays, it is fashionable to create complex polymer resins that facilitate high-resolution 3D printing. This is especially important for applications such as jewelry, dentures, and other areas where small details are crucial.
- 3D printing with a variety of materials is becoming more and more feasible. This approach opens up new possibilities for complex and functional designs, allowing you to create pieces with multiple qualities within a single print.
- In the healthcare industry, there is an increasing focus on creating biocompatible polymers for 3D printing. These materials are needed to create anatomical models, surgical guidance, and implants tailored to individual patients.
- The integration of digital twin technologies is becoming more and more popular. This development makes it possible to create virtual models that are very similar to real products printed on a 3D printer, which allows you to simulate, analyze and optimize processes in virtual conditions.
- One of the key factors driving the development of the sector is the ability to produce and modify products on demand. This model is in line with the broader movement in many industries towards customized and tailored solutions.
- There is a growing trend of collaboration between material suppliers, 3D printer manufacturers, and end-users. This collaboration aims to accelerate innovation in 3D printing and make it easier to create materials that meet specific specifications.
Competitive environment of powders and polymer resins for 3D printing
The competitive landscape in the 3D printing powder and resin market has been dynamic, with several well-known companies competing to provide innovative and cutting-edge 3D printing powder and resin solutions.
- Stratasys
- 3D Systems
- EOS
- Arkema
- Optamec
- Materialise
- HP Inc.
- EnvisionTEC
- ExVan
- Sinterite
- XYZprinting
- DSM
- Evonik
- Formlabs
- carbon
- Renishaw
- Voxeljet
- Proto Laboratory
- Teton 3D
- Prodways
Recent improvements:
July 31, 2023: Optomec announced its vision to embed digital transformation across the company to provide customers with modern capabilities and efficiencies. The focus will be on developing synergies between hardware and software to enable a modern approach to digital automation and digital manufacturing across the entire product portfolio. This will provide customers with a cost-effective method of managing workload and equipment, analyzing data and results, resulting in improved quality and efficiency of the production process.
November 07, 2023: The world's leading additive manufacturing event HP Inc. (Booth D41, Hall 12.1) announced a strategic partnership with INDO-MIM (Indo-MIM Private Limited), one of the world's largest players in the metal injection molding (MIM) industry and a new player in the powder additive manufacturing industry. This collaboration marks a significant step towards the development of metal additive manufacturing technology and the expansion of its application in various industries. Initially, INDO-MIM invested in three cutting-edge HP Metal Jet S100 printers as part of this collaboration, reinforcing its commitment to advancing additive manufacturing worldwide.
3D Printing Powders and Polymer Resins Market Regional Analysis
The Asia-Pacific region accounts for the largest market for 3D printing powders and polymer resins. The Asia-Pacific region accounted for 38% of the global market value. Due to the explosive growth of additive manufacturing (AM) in this area, the Asia-Pacific market is expected to grow at the fastest rate for 3D printing powders and polymer resins. India is projected to have the second largest market share in the Asia-Pacific region after China. The Asia-Pacific region has always served as a hub for global manufacturing, especially in countries like China. The need for 3D printing materials, including powders and resins, has increased in many industries due to the region's huge production capacity. In the Asia-Pacific region, industries such as electronics, automotive, aerospace, and healthcare have been early adopters of 3D printing technology. The market has grown as a result of these industries' need for polymer resins and powders for 3D printing. With a strong focus on research and development, the Asia-Pacific region has become a leader in technical development. As a result, modern 3D printing materials have emerged, which have stimulated the local market.
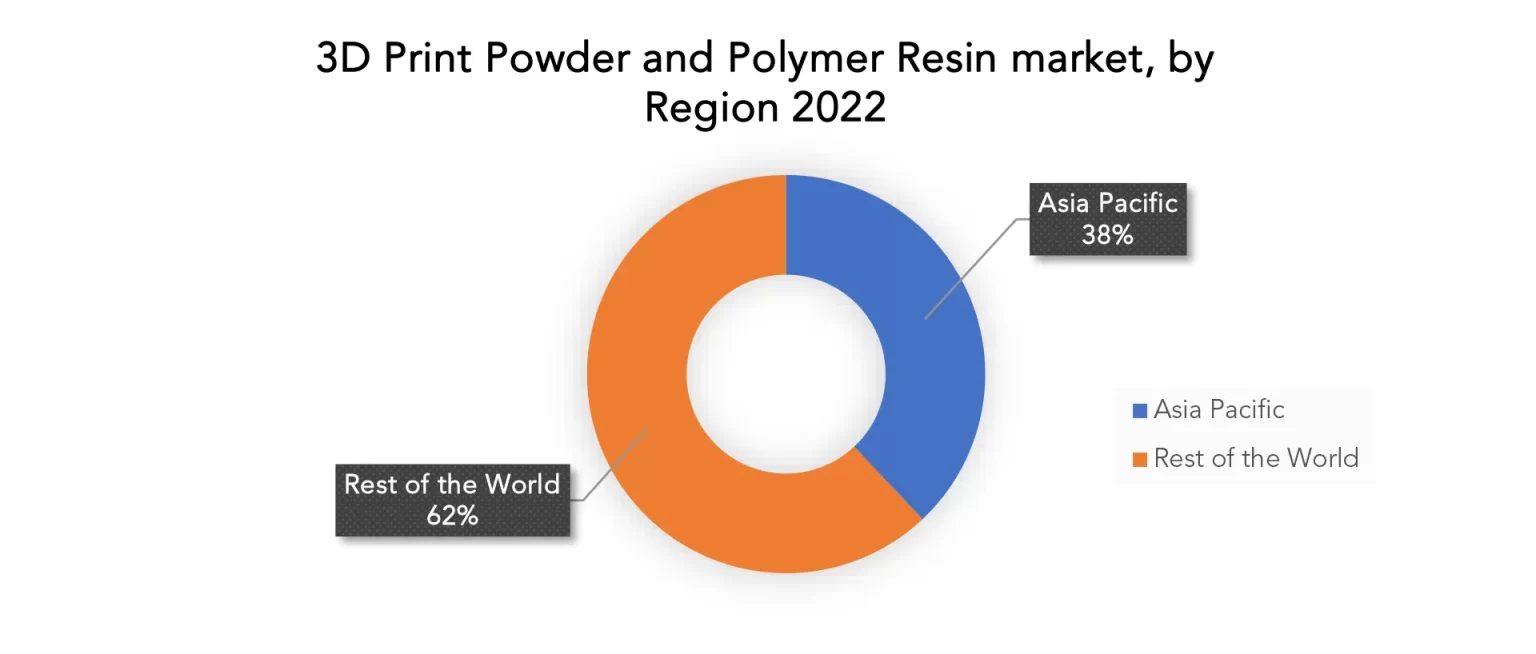
Several countries in the Asia-Pacific region have made efforts and policies to encourage the use of 3D printing and other advanced manufacturing technologies. Support from the government has helped to create a favorable atmosphere for the market. The need for efficient and advanced manufacturing solutions has increased dramatically due to the rapid industrialization and urbanization of the Asia-Pacific region. The customization and complex geometry that 3D printing offers make it perfectly suited to the demands of a changing industrial world. The healthcare sector in Asia Pacific has grown significantly, and the use of 3D printing in areas such as the production of medical devices and personalized treatment plans has increased the demand for related materials. In the global consumer electronics market, the Asia-Pacific region occupies a significant position.
Target Audience of 3D Printing Powders and Polymer Resins Market
- 3D Printer Manufacturers
- Material Suppliers
- End-User Industries
- Research and Development (R&D) Teams
- Government & Regulatory Agencies
- Distributors & Resellers
- Service Bureaus
- Consulting & Market Analysts
- Educational Institutions
- Investors & Venture Capitalists
Market dynamics of 3D printing powders and polymer resins
Driver
Continuous innovation and improvements in 3D printing technologies are driving the market for 3D printing powders and polymer resins.
The speed and accuracy of printing have increased as a result of the development of 3D printing technology. Higher productivity and a wider range of applications in a variety of industries are facilitated by high-resolution printing and shorter production cycles. Subsequently, there was an increased need for a range of powder and resin materials that could meet the performance characteristics of these sophisticated printers. In recent years, multi-material 3D printing has gained popularity, which allows different powders or resins to be used simultaneously in the same printing process. This feature increases the adaptability of 3D printing and allows for the production of more complex and useful end products. To take advantage of the benefits and challenges that multi-material 3D printing presents, manufacturers are actively creating new materials. The future of additive manufacturing is being shaped by a combination of 3D printing and other Industry 4.0 technologies, including robotics, artificial intelligence, and the Internet of Things (IoT). These technologies simplify intelligent manufacturing processes that improve automation, reduce errors, and optimize manufacturing processes. Because of this integration, there is a need for sophisticated powder and polymer materials that can meet the needs of digitally networked manufacturing processes. Specialized materials are becoming increasingly necessary as 3D printing becomes more prevalent in various industries. For example, the aviation industry will require strong and lightweight metal powders, while healthcare may require polymer resins that can be serialized and are biocompatible. The goal of continuous research and development is to create materials with special qualities to solve problems unique to the industry.
Curbing
Limitations on material properties may become a major concern for the 3D printing powders and polymer resins market during the forecast period.
It can be difficult to achieve the desired mechanical qualities such as strength, hardness, and flexibility with some 3D printing materials. High-performance metal alloys and polymers are available, but not for all applications, especially those requiring extreme strength or stability, they can be used appropriately. The heat resistance of many 3D printing materials, especially polymers, can be limited. In applications where components are exposed to high temperatures, such as in the automotive or aerospace industries, this can be crucial. It is still a challenge to develop materials that can withstand high temperatures without breaking too much. In the medical field, where 3D printing is increasingly being used to create medical implants and other devices, ensuring the highest possible biocompatibility is essential. Although the range of 3D printing materials is expanding, it still lacks completeness. Metals, polymers, ceramics, and composites are just a few examples. The limited availability of highly specialized 3D printing materials in some industries limits its application in such areas. Inconsistencies in the quality of materials can arise due to the lack of standardized testing procedures and quality control mechanisms for 3D printing materials. It is difficult for manufacturers to constantly predict and adjust the performance of printed parts due to the lack of uniformity. In order to obtain the appropriate mechanical properties, precision, or polish of the surface, some materials may require lengthy post-processing. The benefits of rapid prototyping and manufacturing, which 3D printing is said to offer, may be outweighed by this extra step. The reuse of 3D printing materials, especially polymers, is more difficult than with traditional manufacturing methods. It is imperative to create effective recycling strategies for 3D printing materials to address sustainability concerns and reduce environmental impact.
possibilities
The continued creation of cutting-edge 3D printing materials opens up new possibilities.
The growing focus on environmental responsibility is in line with the development of sustainable and eco-friendly materials for 3D printing. There are prospects for materials derived from recycled materials, bio-based materials, and materials that generally have less impact on the environment. Complex, multifunctional items can be made with a single print thanks to advances in creating materials suitable for multi-material 3D printing. As a result, applications in robotics, electronics, and other fields that require integrated components are now possible. Creating biocompatible materials for 3D printing is helping the medical industry. There are opportunities to develop materials that are safe and biocompatible enough to be used in the production of anatomical models, prostheses and implants adapted to individual patients. Materials can be tailored to meet the specific needs of several industries, including electronics, automotive, aerospace, and healthcare. For example, the development of biocompatible resins for use in medicine or heat-resistant materials for use in aircraft components. There are opportunities to develop materials with better conductivity, strength, flexibility, and heat resistance, among other characteristics. These materials can be used to produce high-performance components with a wide range of applications. Prototypes and finished products with specific characteristics can be produced thanks to customizable materials, which helps create more specialized and efficient manufacturing processes. This is especially advantageous for industries where special quality materials or unusual geometries are required.
Import & Export 3D Printing Powders & Polymer Resins Market Data
Understanding import and export data is crucial for any player in the 3D printing powder and resin market. This knowledge gives businesses strategic advantages, such as:
- Identification of emerging markets with untapped potential.
- Adapt supply chain strategies to optimize cost efficiencies and market responsiveness.
- Managing competition by assessing the trading dynamics of the main players.
Key takeaways
- Trade Volume Trends: Our report analyzes import and export data over the past five years to identify the most important trends and growth patterns in the global 3D printing powder and polymer resin market. This data-driven research gives readers an in-depth understanding of the market's trajectory.
- Market participants: Gain insight into the leading players in the 3D printing powders and polymer resins trade. Our analysis highlights the key players in the import and export market, from established giants to new contenders.
- Geographic dynamics: Delve into the geographical distribution of trade activities. Find out which regions dominate exports and which control imports and get a complete picture of the industry's global presence.
- Product Distribution: By segmenting data based on 3D printing powder and resin types, we provide detailed insights into trade preferences and changes, enabling businesses to align strategies with the evolving technology landscape.
Import and export data is crucial in reports as it provides insight into global market trends, identifies new opportunities, and informs supply chain management. By analyzing trade flows, businesses can make informed decisions, manage risk, and adapt strategies to changing demand. This data helps the government in policy formulation and trade negotiations, and investors use it to assess market potential. Moreover, import and export data contribute to economic performance, influence product innovation, and promote transparency in international trade, making it an important component of comprehensive and informed analysis.