How are 3D printers used in industrial research and development? Industrial 3D Printer Buying Guide
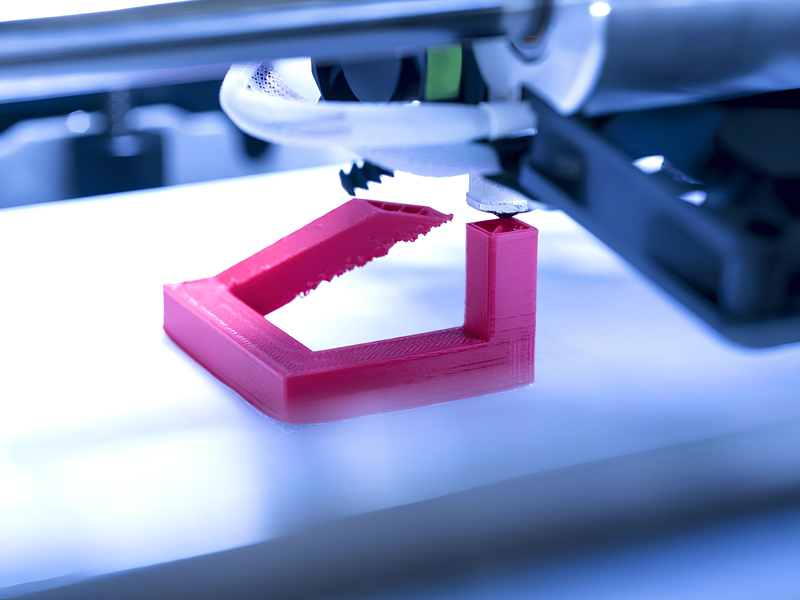
How are 3D printers used in industrial research and development? Industrial 3D Printer Buying Guide
In this article, you will learn how 3D printers are used in different industries and what you should look for when choosing equipment for each industry.
The use of 3D printers for industrial research and development has made it possible to simplify design, increase the efficiency of the manufacturing process, and reduce development time for professionals in many industries. 3D printers play a leading role, ranging from hobbyists designing molds for jewelry production to experts in aerospace and medical printing.
In the hands of a skilled engineer, going from concept to prototype to minimum viable product can look like magic, all thanks to the limitless possibilities that industrial R&D printers offer. As we said earlier, this guide is designed to help you better understand the functions of 3D printers in different industries.
3D Printers for Industrial Products
Manufactured goods depend on the demand for the consumer goods they help to produce. Manufactured goods are classified as either manufactured goods or ancillary goods. Manufacturing goods are used in the manufacture of the final consumer good or product, while ancillary goods help in the manufacturing process of consumer goods such as machinery and machinery.
Companies operating in the industrial goods sector represent a variety of industries, including engineering, construction, defense, aerospace, and construction.
The production of manufactured goods requires a lot of capital investment. Most companies engaged in the production of manufactured goods raise capital by issuing shares and debt, as well as by borrowing from financial institutions. However, since the advent of 3D printers for industrial research and development, the industrial product chain has changed. 3D printers have expanded the production line of most manufacturers involved in the manufacture and distribution of industrial goods.
Has an important part broken down on your car? Spare parts created with 3D printing are becoming a huge asset for both companies and customers! Needless to say, most of the industries listed above rely heavily on rapid prototyping capabilities on 3D printers.
3D Printers for Mold Production
Today, most plastic products in the world are made by injection molding. However, mold making can be prohibitively expensive and time-consuming. Thankfully, molds don't always have to be made of metal — they can be 3D printed. Here are some of the benefits that jewelers, artisans, and general 3D printing enthusiasts get by using industrial R&D 3D printers to print molds.
- Print multiple copies at the same time.
- Opening of our own small-scale production.
- Exact copies. High-resolution 3D printers will keep designs identical without the need to recalibrate between batches.
3D printing molds make the printing process simple, fast, and cost-effective. There are a large number of 3D printers available for designing and creating molds. SLA, LCD, and DLP allow for high accuracy, but have limitations in terms of lifespan and portability. In order to fully enjoy the mold design and creation process, it is recommended to choose FDM technology.
3D Printers for Aerospace
Due to the fact that aircraft parts are usually produced in small batches, the aerospace industry uses 3D printers for most of its production. This technology makes it possible to produce complex parts that are stronger and lighter compared to those made using traditional technologies.
The aerospace industry was one of the first to incorporate 3D printing technology into manufacturing processes. Nowadays, it is still considered the industry with the highest adoption rate of 3D printing technologies.
Additive manufacturing addresses challenges such as reducing fuel consumption by reducing overall fuel weight, which also reduces operating costs and carbon emissions, two of the main challenges faced by airlines.
Industry-agnostic externalities, such as supply chain optimization through decentralized production of parts where they are needed (as opposed to centralized parts production and delivery), also make industrial R&D 3D printers attractive and valuable to aerospace market participants.
Aerospace parts often include internal channels for conformal cooling, internal features, thin walls, and complex curved surfaces. 3D printing processes make it possible to create very complex and lightweight designs with high stability, allowing multiple parts to be combined into a single component.
3D Printers for Automotive Parts
3D printing technology has led to impressive advances in the automotive industry, from the ability to rapidly prototype to the production of virtually complete cars. Automotive giants such as Mitsubishi Chemical or BASF see significant advantages in the use of FDM printing technology in the automotive industry.
The automotive sector is using rapid prototyping with 3D printing more and more. Designers and engineers who are open to innovation implement bold ideas using this technology, thereby expanding the set of engineering benefits and optimizing production processes.
3D printers have a lot of power and can achieve effects that would not be possible with traditional production methods. Automotive components made with FDM technology are lighter, resulting in lower vehicle weight, better performance, and lower energy consumption.
Currently, one of the most popular and most commonly used 3D printing technologies in the automotive industry is FFF (Fused Filament Fabrication). Its advantage is the possibility of using many different materials, similar in properties to plastics.
With the help of a 3D printer, it is possible to create the necessary parts, which allows you to maintain the continuity of production, as well as become independent from external suppliers and optimize production processes.
3D Printers for Medicine
3D printers for industrial research and development have many features in a wide variety of industries. In the field of medicine, 3D equipment has four main applications:
- 3amen of human organ transplants;
- Acceleration of surgical procedures;
- Production of cheaper versions of necessary surgical instruments;
- Improving the lives of those who depend on prosthetic limbs.
With the help of 3D printers, it is possible to produce sterile surgical instruments such as forceps, hemostatic clips, scalpel handles, and other clamps. Off-the-shelf instruments can be used for surgeries on tiny areas without causing unnecessary additional harm to the patient.
3D printing in the medical field is used to make prosthetic limbs that are customized according to the user's needs. Usually, amputees wait weeks or months to get prostheses in the traditional way. 3D printing significantly speeds up the process and also allows for much cheaper products that offer patients the same functionality as traditional prosthetics.
Another application of 3D printers in the medical field is the creation of patient-specific replica organs, on which surgeons can practice before performing complex surgeries. This method has been proven to speed up procedures and minimize patient injury. This type of procedure has been successfully used in surgeries ranging from face transplants to spine surgeries and is beginning to become a common practice.
3D Printers for Military Industry
Many manufacturers offer FDM printers that can efficiently print gun parts. For example, the underparts of the AR-15, Glock frames, AK receivers (which can withstand 2,000 rounds and are only partially 3D printed), and some pistols such as the Songbird (which is mostly 3D-printed).
Many industries that use 3D printing to create their own weapons are moving away from 3D printing and switching to CNC milling instead. Instead of trying to print an entire weapon out of plastic, the unfinished lower receiver parts of the AR-15, known as 80% boxes, are milled, which are used along with other parts to produce finished rifles.
When making these guns only on CNC machines, you need to invest an additional $200 to $400 for additional parts. However, a more likely option for weapons development is the use of 3D printers or industrial installations. Fast and efficient FDM 3D printing process, easily modifiable design makes 3D printers a cost-effective tool for manufacturing.
What kind of equipment is used for industrial research and development
As you already know, 3D printers come in different variants and are optimized for different tasks. SLA, LCD and DLP 3D printers use photopolymer resins as a material. These printers are designed for printing applications where surface smoothness and maximum accuracy are important.
However, printing with photopolymer resins is not suitable for all projects. Sometimes it is worth opting for FDM printing and the use of filament. Below, we will look at the features of the FDM printing process and tell you which FDM 3D printer to choose for industrial research and development.
FDM 3D Printer: Technology and Features
Fused deposition modeling (FDM) is used to make parts from various types of plastic, including high-temperature filaments or filaments with various fillers (Carbon, Glass, and others). A filament of molten thermoplastic material is fed from the coil through the printer extruder head and pushed out of the nozzle onto the work surface.
The computer-controlled printhead of the printer moves in two dimensions to form each layer of the part. There are many options for FDM printers on the market today for industrial research and development.
How to Choose an FDM 3D Printer
When buying an industrial 3D printer, there are several factors to consider first. We invite you to familiarize yourself with the list of features and characteristics that you should pay attention to when purchasing industrial 3D equipment.
Detail Size
Determining the size of the parts that you will regularly print on your 3D printer requires an in-depth knowledge of customer requests or manufacturing needs. If your day-to-day workload consists of printing large parts, it's a good idea to carefully select equipment that not only has a large working area, but also allows you to maintain production rates.
Trusted Brand
There are many brands and a limited number of reviews and testimonials that users leave on industrial-grade equipment. It is necessary to conduct brand analysis on your own in order to have confidence in the equipment you are purchasing. Here are a few questions to focus on when choosing an industrial 3D printer brand:
- How long has the manufacturer of the 3D printer you are going to buy from?
- What customer testimonials confirm their brand identity?
- Are they considered the best brand among industry professionals and experts?
- Do they offer hardware at a price that matches the performance, efficiency, and durability you need from a device?
Machine Safety Configuration
Safety first. You should be careful not to purchase anything that could jeopardize your business. Many people don't bother to check the safety measures when using a particular 3D printer for industrial research and development. If you are new to using an FDM printer, follow all the instructions given in the manual as the hardware may vary.
Print Resolution Requirements
FDM 3D printers are available in a variety of variants, shapes and sizes, optimized for suitable design and resolution. Most often, the manufacturer's line includes equipment that is optimized to perform the tasks of a particular industry. For example, there is equipment for the medical or jewelry industry, rapid prototyping, or the production of parts with tight tolerances in the energy, military, and aerospace industries.
Reasonable cost
Equipment prices vary depending on the needs and desires of the client. FDM equipment often costs less than photopolymer 3D printers with a similar printing area. A clear budget for the purchase will allow you to narrow down your choices.
After-sales service capability
Any equipment requires regular maintenance and sometimes repairs. If the manufacturer offers technical support in your area, the procedure for replacing consumables and repairs will be quick and timely. In addition, it is worth paying attention to having your own support center or the ability to contact the dealer at any time. The technical support service allows you to solve any questions that arise regarding the operation and maintenance of the equipment.
Equipment lifespan
Most industrial R&D 3D printers have a lifespan of 5 to 10 years. While most 3D printers do not come with a refund or after-sales privilege 1 or 2 years after purchase, purchasing an industrial 3D printer from a reputable manufacturer guarantees that the equipment will be in good condition for at least five years.
However, it is important to note that the estimated lifespan of a high-resolution 3D printer can change at any time depending on external factors. How you use your machine will determine how long it will last. If you regularly leave your industrial FDM 3D printer dirty, don't expect a ten-year life expectancy to persist.
Equipment Maintenance Cost
Using 3D printers for industrial research and development for a long time can cause some mechanical parts to fail after just a few months of use. If they are not updated in time, the final quality of the printed parts will deteriorate.
Machine maintenance is necessary and may incur additional costs as some parts, such as the nozzle, may require a complete replacement of the assembly. Before buying, you need to calculate how much of the budget you are willing to spend on the maintenance of your device so as not to lose print quality.
My affialite link: https://bigmoney.vip/?ref=3000
- Equipment_Maintenance_Cost
- Equipment_lifespan
- After-sales_service_capability
- Print_Resolution_Requirements
- Machine_Safety_Configuration
- How_to_Choose_an_FDM_3D_Printer
- FDM_3D_Printer:_Technology_and_Features
- What_kind_of_equipment_is_used_for_industrial_research_and_development
- 3D_Printers_for_Military_Industry
- 3D_Printers_for_Medicine
- 3D_Printers_for_Automotive_Parts
- 3D_Printers_for_Aerospace
- 3D_Printers_for_Mold_Production
- 3D_Printers_for_Industrial_Products
- How_are_3D_printers_used_in_industrial_research_and_development?_Industrial_3D_Printer_Buying_Guide
- Arts
- Business
- Computers
- Games
- Health
- Home
- Kids and Teens
- Money
- News
- Recreation
- Reference
- Regional
- Science
- Shopping
- Society
- Sports
- Бизнес
- Деньги
- Дом
- Досуг
- Здоровье
- Игры
- Искусство
- Источники информации
- Компьютеры
- Наука
- Новости и СМИ
- Общество
- Покупки
- Спорт
- Страны и регионы
- World