Robotics
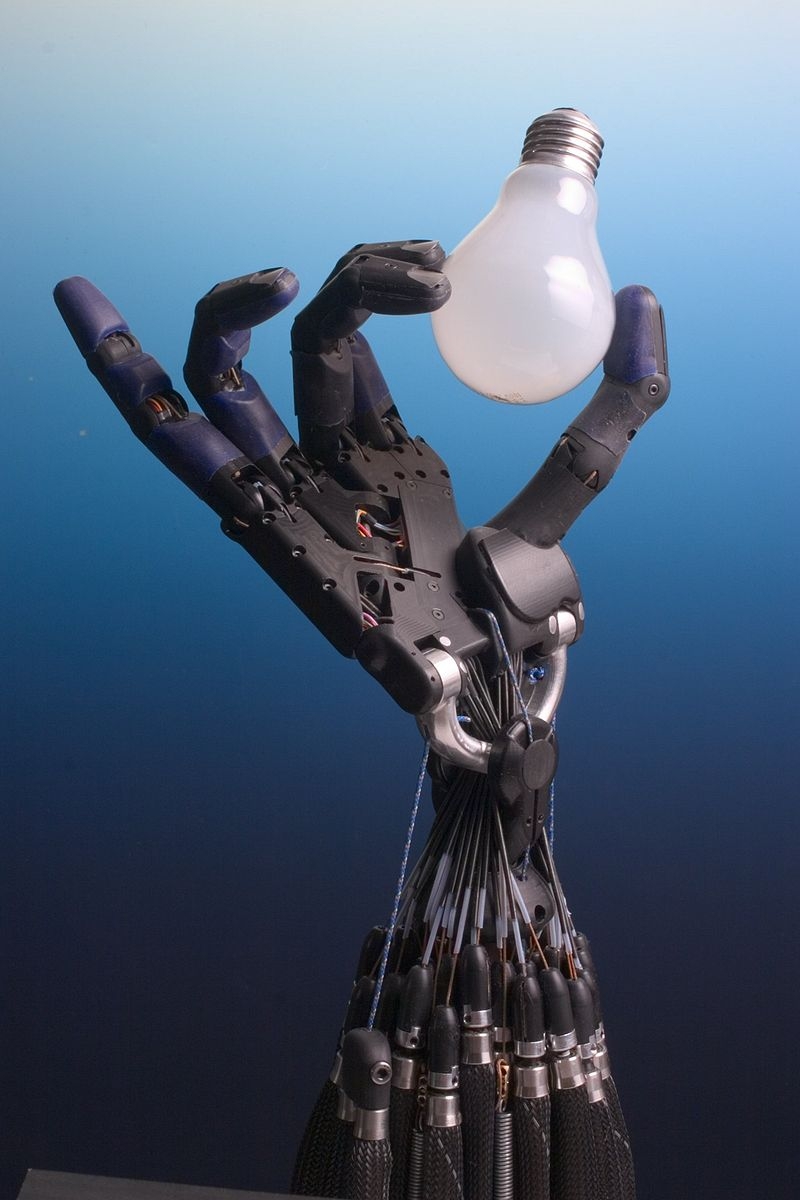
Robotics is an applied science that deals with the development of automated technical systems and is the most important technical basis for the development of production.
Robotics draws on disciplines such as electronics, mechanics, cybernetics, telemechanics, mechatronics, computer science , as well as radio engineering and electrical engineering. There are construction, industrial, household, medical, aviation and extreme (military, space, underwater) robotics.
Etymology of the term
The word "robotics" was first used in print by Isaac Asimov in the science fiction story "Liar", published in 1941.
The word "robotics" is based on the word " robot ", coined in 1920 by Czech writer Karel Čapek and his brother Josef for Karel Čapek's science fiction play R.U.R. (Rossum's Universal Robots), first staged in 1921 and was a hit with audiences. In it, the owner of the factory organizes the production of many androids , which at first work without rest, but then rebel and destroy their creators.
History of the industry
Some ideas that later formed the basis of robotics appeared in ancient times - long before the introduction of the terms listed above. The remains of moving statues made in the 1st century BC have been found. Homer's Iliad says that the god Hephaestus made talking maids out of gold, giving them intelligence (that is, in modern language, artificial intelligence) and strength. The ancient Greek mechanic and engineer Archytas of Tarentum is credited with creating a mechanical pigeon capable of flight (c. 400 BC). More than two thousand years ago, Heron of Alexandria created the “Singing Bird” water machine and a number of systems of movable figures for ancient temples. In 270, the ancient Greek inventor Ctesibius invented a special water clock, called the clepsydra (or “stealing time”), which, with its ingenious device, aroused considerable interest among contemporaries. In 1500, the great Leonardo da Vinci developed a mechanical device in the form of a lion, which was supposed to reveal the coat of arms of France when the king entered the city. In the 18th century, the Swiss watchmaker P. Jaquet-Droz created a mechanical doll called “The Scribe,” which could be programmed using cam drums to write text messages containing up to 40 letters. In 1801, the French merchant Joseph Jacquard introduced an innovative loom design at the time, which could be “programmed” using special cards with holes to reproduce repeating decorative patterns on woven fabrics. At the beginning of the 19th century, this idea was borrowed by the English mathematician Charles Babbage to create one of the first automatic computers. Around the 30s of the 20th century , androids appeared that implemented elementary movements and were able to pronounce the simplest phrases upon human command. One of the first such developments was the design of the American engineer D. Wexley, created for the World Exhibition in New York in 1927.
In the 50s of the 20th century, mechanical manipulators for working with radioactive materials appeared. They were able to copy the hand movements of the operator, who was in a safe place. By 1960, the development of remotely controlled wheeled platforms with a manipulator, a television camera and a microphone was carried out for examination and collection of samples in areas of high radioactivity.
The widespread adoption of industrial numerically controlled machine tools has stimulated the creation of programmable manipulators used for loading and unloading machine tools. In 1954, the American engineer D. Devol patented a method for controlling a loading and unloading manipulator using replaceable punched cards , as a result, in 1956, together with D. Engelberger, he created the world's first industrial company, Unimation ( Unimation from Universal Automation) for the production of industrial robotics. In 1962, the first industrial robots in the United States, Versatran and Unimate, were released, and some of them are still functioning, having surpassed the threshold of 100 thousand hours of working life. While in these early systems the cost ratio between electronics and mechanics was 75% to 25%, this has now been reversed. At the same time, the final cost of electronics continues to decline steadily. The advent of low-cost microprocessor control systems in the 1970s, which replaced specialized robot control units with programmable controllers, helped reduce the cost of robots by approximately three times. This served as an incentive for their mass distribution throughout all sectors of industrial production.
A lot of similar information is contained in the book “Robotics: History and Prospects” by I. M. Makarov and Yu. I. Topcheev , which is a popular and detailed story about the role that robots have played (and will still play) in the history of the development of civilization.
The most important classes of robots
You can use several approaches to classifying robots - for example, by area of application, by purpose, by method of movement, etc. By area of main application, we can distinguish industrial robots, research robots, robots used in teaching, and special robots.
The most important classes of general purpose robots are manipulative and mobile robots.
A manipulation robot is an automatic machine (stationary or mobile), consisting of an actuator in the form of a manipulator , which has several degrees of mobility, and a program control device, which serves to perform motor and control functions in the production process. Such robots are produced in floor-mounted , suspended and gantry versions. They are most widespread in the mechanical engineering and instrument-making industries.
A mobile robot is an automatic machine that has a moving chassis with automatically controlled drives. Such robots can be wheeled , walking and tracked (there are also crawling , swimming and flying mobile robotic systems, see below).
Robot components
Drives
- DC Motors : Currently, most robots use electric motors , which can be of several types.
- Stepper Motors : As the name suggests, stepper motors do not spin freely like DC motors. They rotate step by step to a certain angle under the control of the controller. This allows you to do without a position sensor, since the angle at which the turn was made is known to the controller; Therefore, such motors are often used in many robot drives and CNC machines.
- Piezo Motors : A modern alternative to DC motors are piezo motors, also known as ultrasonic motors. The principle of their operation is very original: tiny piezoelectric legs, vibrating at a frequency of more than 1000 times per second, force the motor to move in a circle or straight line. The advantages of such engines are high nanometric resolution, speed and power, incommensurate with their size. Piezo motors are already available commercially and are also used on some robots.
- Air Muscles : Air muscles are a simple yet powerful device for providing traction. When pumped with compressed air, muscles can contract up to 40% of their length. The reason for this behavior is the weaving visible from the outside, which causes the muscles to be either long and thin or short and thick. Since their mode of operation is similar to that of biological muscles, they can be used to produce robots with muscles and skeletons similar to those of animals.
- Electroactive polymers : Electroactive polymers are a type of plastic that changes shape in response to electrical stimulation. They can be designed in such a way that they can bend, stretch or contract. However, at present there are no EAPs suitable for the production of commercial robots, since all existing samples of them are ineffective or fragile.
- Elastic nanotubes : This is a promising experimental technology in the early stages of development. The absence of defects in nanotubes allows the fiber to elastically deform by several percent. The human biceps can be replaced with a wire made of this material with a diameter of 8 mm. Such compact “muscles” could help robots in the future overtake and jump over humans.
Sensors
- Touch sensors .
- Light sensors .
- Gyroscope sensor .
- Distance sensor .
- Echo sounder and other sensors depending on the purpose of the robot.
Ways to move
Wheeled and tracked robots
The most common robots of this class are four-wheeled and tracked robots . Robots are also being created with a different number of wheels; in this case, it is often possible to simplify the design of the robot, as well as give it the ability to work in spaces where a four-wheeled design is ineffective.
Two-wheeled robots, as a rule, use certain gyroscopic devices to determine the angle of inclination of the robot body and generate the appropriate control voltage supplied to the robot drives (in order to ensure that they maintain balance and perform the necessary movements) . The problem of maintaining the balance of a two-wheeled robot is related to the dynamics of an inverse pendulum. Many similar “balancing” devices have been developed. Such devices include Segway , which can be used as a robot component; for example, the Segway is used as a transport platform in the Robonaut robot developed by NASA.
Single-wheeled robots are in many ways a development of ideas associated with two-wheeled robots. To move in 2D space, a ball driven by several drives can be used as a single wheel. Several designs of such robots already exist. Examples include the ballbot developed at Carnegie Mellon University , the BallIP ballbot developed at Tohoku Gakuin University or the Rezero ballbot developed at the Swiss Higher Technical School . These types of robots have some advantages associated with their elongated shape, which may allow them to integrate better into the human environment than is possible for some other types of robots.
There are a number of prototypes of spherical robots. Some of them use rotation of the internal mass to organize movement. Robots of this type are called in English spherical orb robots orb bot and English ball bot.
A number of designs of mobile wheeled robots use roller-carrying wheels of the “omnidirectional” type (“ omnidirectional wheels ”); such robots are characterized by increased maneuverability.
To move on uneven surfaces, grass and rocky terrain, six-wheeled robots are being developed , which have more traction compared to four-wheeled ones. The tracks provide even greater traction. Many modern combat robots, as well as robots designed to move over rough surfaces, are designed as tracked vehicles. At the same time, it is difficult to use such robots indoors, on smooth surfaces and carpets. Examples of such robots are the English robot developed by NASA . Urban Robot (“Urbie”), iRobot -developed Warrior and PackBot robots .
Walking robots
Moving a robot using its “legs” is a complex dynamic problem. A number of robots have already been created that move on two legs, but these robots cannot yet achieve such stable movement as is inherent in humans. Many mechanisms have also been created that move on more than two limbs. Attention to such structures is due to the fact that they are easier to design. Hybrid options are also offered (such as the robots from the movie “ I, Robot ”, capable of moving on two limbs while walking and on four limbs while running).
Robots that use two legs tend to move well on the floor, and some designs can navigate stairs. Navigating rough terrain is a challenging task for this type of robot. There are a number of technologies that allow walking robots to move:
- Servo drive + hydromechanical drive is an early technology for constructing walking robots, implemented in a number of models of experimental robots manufactured by General Electric in the 1960s. The first GE project embodied in metal using this technology and, in all likelihood, the world’s first walking robot for military purposes was the “four-legged transporter” Walking Truck (the machine has robotic limbs, control is carried out by a person located directly in the cabin).
- ZMP technology: ZMP ( English zero moment point , “zero moment point”) is an algorithm used in robots like Honda ’s ASIMO . The on-board computer controls the robot in such a way that the sum of all external forces acting on the robot is directed towards the surface on which the robot is moving. Thanks to this, no torque is created, which could cause the robot to fall. This type of movement is not typical for humans, as can be seen by comparing the manner of movement of the ASIMO robot and a person.
- Jumping robots: In the 1980s, Professor Marc Raibert of the MIT Leg Laboratory developed a robot that could maintain balance by jumping using only one leg. The robot's movements are reminiscent of human movements on a pogo stick trainer. The algorithm was subsequently extended to mechanisms using two and four legs. Such robots have demonstrated running abilities and the ability to perform somersaults. Robots moving on four limbs demonstrated running, trotting , gait , and skipping.
- Adaptive algorithms for maintaining balance. They are mainly based on calculating the deviations of the instantaneous position of the robot’s center of mass from a statically stable position or some predetermined trajectory of its movement. In particular, similar technology is used by the walking robot carrier Big Dog. When moving, this robot maintains a constant deviation of the current position of the center of mass from the point of static stability , which entails the need for a peculiar positioning of the legs (“knees in” or “push-pull”), and also creates problems with stopping the machine in one place and practicing transitional walking modes . An adaptive algorithm for maintaining stability can also be based on maintaining a constant direction of the velocity vector of the system’s center of mass, however, such techniques are effective only at sufficiently high speeds. The greatest interest for modern robotics is the development of combined methods for maintaining stability, combining the calculation of the kinematic characteristics of the system with highly effective methods of probabilistic and heuristic analysis.
Other methods of movement
- Flying robots. Most modern aircraft are flying robots controlled by pilots. The autopilot is capable of controlling the flight at all stages - including takeoff and landing. Flying robots also include unmanned aerial vehicles (UAVs; cruise missiles are an important subclass of them ). Such devices are, as a rule, light in weight (due to the absence of a pilot) and can carry out dangerous missions; some UAVs are capable of firing at the operator's command. UAVs are also being developed that can fire automatically. In addition to the method of movement used by airplanes, flying robots also use other methods of movement - for example, similar to those used by penguins , stingrays , jellyfish ; Festo 's Air Penguin, Air Ray and Air Jelly robots use this method of movement, or they use insect- like flight methods , such as RoboBee.
- Crawling robots. There are a number of developments of robots that move like snakes, worms, slugs; in this case, to implement movement, the robot can use friction forces (when moving on a rough supporting surface) or changes in surface curvature (in the case of a smooth surface of variable curvature). It is assumed that this method of movement may give them the ability to move in narrow spaces; in particular, it is proposed to use such robots to search for people under the rubble of collapsed buildings. Snake-like robots have also been developed that can move in water; An example of such a design is the Japanese robot ACM-R5.
- Robots moving on vertical surfaces. When designing them, various approaches are used. The first approach is to design robots that move like a person climbing a wall covered with ledges. An example of such a design is the Capuchin robot developed at Stanford University. Another approach is to design robots that move like geckos and are equipped with vacuum suction cups. Examples of such robots are Wallbot and Stickybot.
- Floating robots. There are many designs of robots that move in water, imitating the movements of fish . According to some estimates, the efficiency of such propulsion can be 80% higher than the efficiency of propulsion using a propeller. In addition, such structures produce less noise and are also characterized by increased maneuverability. This is the reason for the high interest of researchers in robots that move like fish. Examples of such robots are the Robotic Fish robot developed at the University of Essex and the Tuna robot developed by the Institute of Field Robotics (English) to study and simulate the mode of movement characteristic of tuna. There are also developments of floating robots of other designs. Examples are robots from Festo: Aqua Ray , which imitates the movements of a stingray , and Aqua Jelly , which imitates the movements of a jellyfish .
Control systems
By controlling a robot we mean solving a set of problems related to adapting the robot to the range of tasks it solves, programming movements, and synthesizing a control system and its software.
Based on the type of control, robotic systems are divided into:
- Biotechnical:
- command (push-button and lever control of individual parts of the robot);
- copying (repetition of human movement, it is possible to implement feedback that transmits the applied force, exoskeletons);
- semi-automatic (control of one command element, for example, a handle, the entire kinematic circuit of the robot);
- Automatic:
- software (function according to a predetermined program, mainly designed to solve monotonous problems in constant environmental conditions);
- adaptive (solve standard problems, but adapt to operating conditions);
- intelligent (the most developed automatic systems);
- Interactive:
- automated (alternation of automatic and biotechnical modes is possible);
- supervisory (automatic systems in which a person performs only target functions);
- interactive (the robot participates in a dialogue with a person on choosing a behavioral strategy, and as a rule, the robot is equipped with an expert system that can predict the results of manipulations and give advice on choosing a goal).
Among the main tasks of robot control are the following:
- planning provisions;
- movement planning;
- planning of forces and moments;
- dynamic accuracy analysis;
- identification of kinematic and dynamic characteristics of the robot.
In the development of methods for controlling robots, the achievements of technical cybernetics and the theory of automatic control are of great importance .
Areas of application
The average number of robots in the world in 2017 is 69 per 10,000 workers. The largest number of robots is in South Korea - 531 per 10,000 workers, Singapore - 398, Japan - 305, Germany - 301.
Education
Robotic systems are also popular in the field of education as modern high-tech research tools in the field of automatic control theory and mechatronics . Their use in various educational institutions of secondary and higher vocational education makes it possible to implement the concept of “ project-based learning ”, which forms the basis of such a large joint educational program of the United States and the European Union as ILERT . The use of the capabilities of robotic systems in engineering education makes it possible to simultaneously develop professional skills in several related disciplines: mechanics , control theory , circuit design , programming , information theory . The demand for complex knowledge contributes to the development of connections between research teams. In addition, already in the process of specialized training, students are faced with the need to solve real practical problems.
Popular robotic systems for educational laboratories:
- Mechatronics Control Kit
- Festo Didactic
- LEGO Mindstorms
- fischertechnik .
- educational kits based on Arduino
There are others. The Moscow Center for Pedagogical Excellence compared the most popular platforms and robotic constructors.
The profession of mobile roboticist is included in the list of the 50 most popular professions according to the Ministry of Labor of the Russian Federation
It is predicted that the sales volume of robots for education and science in 2016-2019. will be 8 million units.
Robotics is included in the school curriculum for grades 7-9
Industry
Robots have been successfully used in manufacturing for decades. Robots successfully replace humans when performing routine, energy-intensive, and dangerous operations. Robots do not get tired, they do not need breaks for rest, water and food. Robots do not demand higher wages and are not members of trade unions.
As a rule, industrial robots do not have artificial intelligence. It is typical to repeat the same movements of the manipulator according to a rigid program.
Great strides have been made, for example, in the use of robots on conveyors of automobile factories. There are already plans for enterprises in the automotive industry, where all processes of assembling cars and transporting semi-finished products will be carried out by robots, and people will only control them.
In the nuclear and chemical industries, robots are widely used when working in radioactive and chemically hazardous environments.
A robot has been created for automated diagnostics of the condition of power lines, consisting of an unmanned helicopter and a device for landing and moving along a lightning protection cable.
In 2016, 1.8 million robots were used in industry across the world, and it is predicted that by 2020 their number will exceed 3.5 million.
It is predicted that the sales volume of robots in 2016-2019. for use in logistics, construction and demolition will be 177 thousand units.
Agriculture
The first robots that provide automated care for crops are being used in agriculture. The first robotic greenhouses for growing vegetables are being tested.
It is predicted that the sales volume of robots in 2016-2019. for use in agriculture will be 34 thousand units.
One of the dynamically developing areas of robotics development in recent years is the use of autonomous control systems for agricultural transport. Experts divide them into two classes: parallel driving systems or direction indicators and control systems based on artificial intelligence (AI).
The practice of using parallel driving systems goes back about 25 years. Navigation in them is carried out using a satellite signal. Their disadvantage is the so-called “blindness”. The system responds only to objects pre-marked on the route. If an unexpected obstacle appears in front of the equipment (a person, a power pole, etc.), the risk of an incident is very high. In addition, there are known problems with parallel driving systems associated with inaccuracy of the satellite signal, the need to install additional stations and subscribe to paid services.
The second class is a new generation of systems where control is carried out on the basis of artificial intelligence and is dynamically developing. Despite the modest composition of players, according to industry analysts, the main events will unfold in this zone in the near future.
Experts believe that AI-based systems allow:
- Reduce harvesting time by an average of 25%
- Reduce direct crop losses by up to 13%
- Reduce fuel consumption during harvesting by up to 5%
- Increase the operator’s daily output by up to 25%
Medicine
In medicine, robotics is used in the form of various exoskeletons that help people with musculoskeletal disorders. Miniature robots are being developed for implantation into the human body for medical purposes: pacemakers, information sensors, etc.
The first robotic surgical complex for performing operations in urology has been developed in Russia.
It is predicted that the sales volume of robots in 2016-2019. for medical use will be 8 thousand units.
Cosmonautics
Robotic manipulators are used in spacecraft. For example, in the Orlets observation spacecraft there was a so-called capsule machine that loaded small-sized descent capsules with film. Rovers, such as the Lunokhod and the Mars rover, can be considered as interesting examples of mobile robots.
Sports
The first World Robot Football Championship was held in Japan in 1996 (see RoboCup ).
Transport
According to forecasts, the production of fully automated passenger cars with autopilot in 2025 will amount to 600 thousand units.
Military affairs
The first fully autonomous robots for military use have already been developed. International negotiations began on their ban.
Fire safety
Fire robots (robotic installations) are actively used in fire fighting. The robot is capable of independently detecting a fire, calculating coordinates, and directing a fire extinguishing agent to the center of the fire without human assistance. As a rule, these robots are installed at explosive sites.
Social consequences of robotization
It is noted that hourly wages for manual labor in developed countries are increasing by about 10-15% per year, and the costs of operating robotic devices are increasing by 2-3%. At the same time, the level of hourly pay for an American worker exceeded the cost of an hour of work for a robot around the mid-70s of the 20th century. As a result, replacing a person in the workplace with a robot begins to bring net profit in about 2.5-3 years.
Robotization of production reduces the competitive advantage of economies with cheap labor and causes the movement of skilled labor from manufacturing to the service sector. In the future, mass professions (drivers, salespeople) will be robotized. In Russia, up to half of jobs can be replaced.
Every single increase in the number of robots used in US industry between 1990 and 2007 resulted in the elimination of six human jobs. Each new robot per thousand jobs reduces the average wage in the US economy by an average of half a percent.
In Russia, robots are used mainly in the automotive industry and microelectronics.
- Arts
- Business
- Computers
- Jogos
- Health
- Início
- Kids and Teens
- Money
- News
- Recreation
- Reference
- Regional
- Science
- Shopping
- Society
- Sports
- Бизнес
- Деньги
- Дом
- Досуг
- Здоровье
- Игры
- Искусство
- Источники информации
- Компьютеры
- Наука
- Новости и СМИ
- Общество
- Покупки
- Спорт
- Страны и регионы
- World